Graphite electrodes are an integral part of important industrial processes such as arc steelmaking and metal smelting. They are composed of graphite powder and calcined blanks, in which the impregnation weight gain rate of the calcined blanks is a crucial parameter. This article will explore the importance of impregnation weight gain in graphite electrode manufacturing and the key factors in determining appropriate impregnation weight gain.
1. Basic process of graphite electrode manufacturing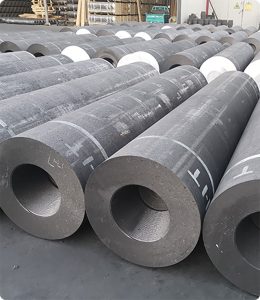
Before we discuss the impregnation weight gain rate in depth, let us briefly understand the basic manufacturing process of graphite electrodes. The manufacturing process of graphite electrodes includes the following main steps:
Mixing and pressing of graphite powder: Carefully selected graphite powder is mixed with a binder and then pressed into a green body under high pressure. This green body is usually called a fired body.
Roasting of the green body: Roasting is to heat the green body to a high temperature to remove impurities and binders in it, making it dense and stable at high temperatures.
Impregnation of the green body: After firing, the green body needs to be immersed in a liquid material, usually pyro pitch or other conductive substances. This step determines the conductivity and thermal stability of the electrode.
Re-baking: The impregnated green body needs to be roasted again to solidify the impregnated material and ensure that it has the required physical and chemical properties.
Machining and Trimming: Finally, the electrode body needs to be machined and trimmed to meet specific specifications and requirements.
In this process, the impregnation weight gain rate of the calcined blank is a key parameter, which directly affects the performance and life of the electrode.
2. The importance of impregnation weight gain rate
The impregnation weight gain rate refers to the percentage increase in the weight of the calcined blank after impregnation relative to the weight before roasting. It is an important parameter because it is directly related to the electrical conductivity, thermal conductivity, mechanical strength and fire resistance of the electrode. The following is the importance of maceration weight gain:
2.1 Conductivity
The impregnation weight gain rate has a significant impact on the conductivity of the electrode. The conductive material (usually pyro-pitch) in the impregnated green body fills the gaps in the graphite structure, thereby increasing the conductivity. Proper impregnation weight gain rate ensures low resistance of the electrode, which is very important for high current applications such as arc steelmaking.
2.2 Thermal conductivity
The thermal conductivity of graphite electrodes is crucial for heat transfer in metallurgical processes. Adjustment of the impregnation weight gain rate can affect the thermal conductivity of the electrode, so for thermal conduction sensitive applications, such as blast furnace operations, the impregnation weight gain rate must be carefully controlled.
2.3 Mechanical strength
Appropriate impregnation weight gain rate can also increase the mechanical strength of the electrode. Mechanical strength refers to the electrode’s ability to resist bending and extrusion under high temperature and high pressure environments. This is crucial for the long-term use of the electrodes in metallurgical furnaces.
2.4 Fire resistance
Impregnated electrodes often operate in extremely high temperature environments. Appropriate impregnation weight gain rate can improve the fire resistance of the electrode and extend its service life.
3. Determine the appropriate weight gain rate for maceration
Determining the appropriate impregnation weight gain rate requires consideration of several factors, including application requirements, material properties and process conditions. Here are some key factors:
3.1 Application requirements
First, understand the specific application the electrode will be used for. Different applications require different performance characteristics. For example, blast furnace operation may require electrodes with high electrical and thermal conductivity, while other applications may be more concerned with mechanical strength.
3.2 Graphite quality
The quality of graphite powder has an important influence on the impregnation weight gain rate. The quality of the powder must be strictly controlled to ensure consistent infusion results.
3.3 Impregnated materials
The nature of the impregnated material and the impregnation process are also important factors. The selection and treatment of impregnated materials will directly affect the impregnation weight gain rate.