Introduce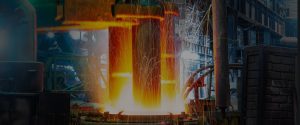
In the production process of graphite electrodes, graphite anodes and high-density and high-strength graphite products, in order to reduce the porosity and increase the density and strength of the product, the baked semi-finished products need to be impregnated. If the impregnated products are directly fed into the graphitization furnace, the production efficiency of the graphite chemical method will be reduced, power consumption will be increased, the environment will be polluted, and working conditions will be deteriorated.
In the production process of graphite electrodes, graphite anodes and high-density and high-strength graphite products, in order to reduce the porosity and increase the density and strength of the product, the baked semi-finished products need to be impregnated. If the impregnated products are directly fed into the graphitization furnace, the production efficiency of the graphite chemical method will be reduced, power consumption will be increased, the environment will be polluted, and working conditions will be deteriorated. Therefore, it is necessary to put the impregnated product into the calcining furnace again to carbonize the impregnating agent under mild conditions. Practice has proven that secondary roasting of impregnated products is beneficial to improving the quality of graphitized products and the economic benefits of enterprises.
The main difference between secondary roasting and primary roasting is that the product after secondary roasting is impregnated after primary roasting. The product geometry is fixed and there will be no overall deformation during secondary firing. In addition, the thermal conductivity of the impregnated product is higher than that of the original product, and the heat treatment speed of the second roasting is faster than that of the first roasting, with the final temperature being only 700°C. Therefore, if the first roasting curve is 320h, the second roasting curve is generally 138h. Another feature is that the second roasting does not require fillers.
The main technical feature of the secondary baking of the impregnated electrode is that when the calcined product reaches 400-500°C, part of the asphalt is heated and melted out of the impregnated electrode. If an ordinary tunnel kiln is used for roasting, it will flow to the surface of the kiln car and the other part will be released as flammable gas. Therefore, it is necessary to use a roasting device that allows the combustible materials escaping from the electrode to be burned directly in the kiln.
Compared with direct graphitization of impregnated products, the advantages of impregnated products after secondary roasting and then graphitization are as follows:
(1) It can improve the yield of the graphitization process and shorten the graphitization time;
(2) It can reduce the cost of the graphitization process. Electricity consumption;
(3) It can greatly reduce the harmful gases from asphalt decomposition emitted during the graphitization process and improve the production environment;
(4) It is beneficial to increase the coking residual carbon rate of the impregnating agent asphalt and increase the volume density of the product.